When your property suffers water damage, removing excess moisture is crucial to prevent further deterioration and mold growth. At First Coast Contracting, we understand how vital swift, effective dehumidification is to restoring structural integrity. Below, we unpack the most effective dehumidification methods employed in modern water damage restoration—offering insights grounded in current industry practices and technology.
Table of Contents
Why Dehumidification Matters After Water Damage
Right after a flood, leak, or heavy storm, affected materials—like drywall, insulation, flooring, and wood—can retain excessive moisture. That lingering damp environment encourages mold growth, warping, swelling, and eventual breakdown of materials. Without properly removing water vapor from the space, drying efforts are incomplete and restoration takes much longer.
Rapid dehumidification removes moisture from the air and materials efficiently. By exchanging humid indoor air with drier conditions, these systems support drying equipment like air movers and heating elements. They also reduce humidity faster than time alone, improving indoor air quality and safeguarding health.
Refrigerant Dehumidifiers
How They Work
Refrigerant dehumidifiers are the industry standard for post-water-damage drying. These machines condense moisture from the air by cooling it to its dew point. Warm, humid air moves over cold evaporator coils; moisture condenses into liquid water, which drains away. The dehumidified air then passes over a warm condenser coil and is returned to the space more dry and slightly warmer.
Ideal Use
These units are powerful in most indoor environments—from basements to crawlspaces to living rooms. They maintain a balance of airflow, temperature, and humidity. For many jobs, refrigerant systems are the first line of defense once surface water is removed.
Benefits and Limitations
Refrigerant dehumidifiers excel in temperatures above 60°F (16°C). However, they lose efficiency in colder environments—coils can ice over, stopping moisture removal. On the flip side, they produce heat, which can aid evapotranspiration but also risk overheating in sensitive settings.
Desiccant Dehumidifiers
How They Operate
Instead of cooling air, desiccant dehumidifiers use a drying agent—typically silica gel—to actively absorb moisture. The air flows through a rotor coated with the desiccant; as it passes, water vapor is captured. The moisture-laden rotor then goes through a regeneration cycle, where heat removes that moisture and vents it away. The process renews the drying material continuously.
Where They Shine
Desiccant systems handle low-humidity and low-temperature scenarios exceptionally well. In unheated structures, cold climates, or during winter, they outperform refrigerant units. Their capability to reduce humidity to very low levels also helps in deep drying of porous materials like wood and plaster.
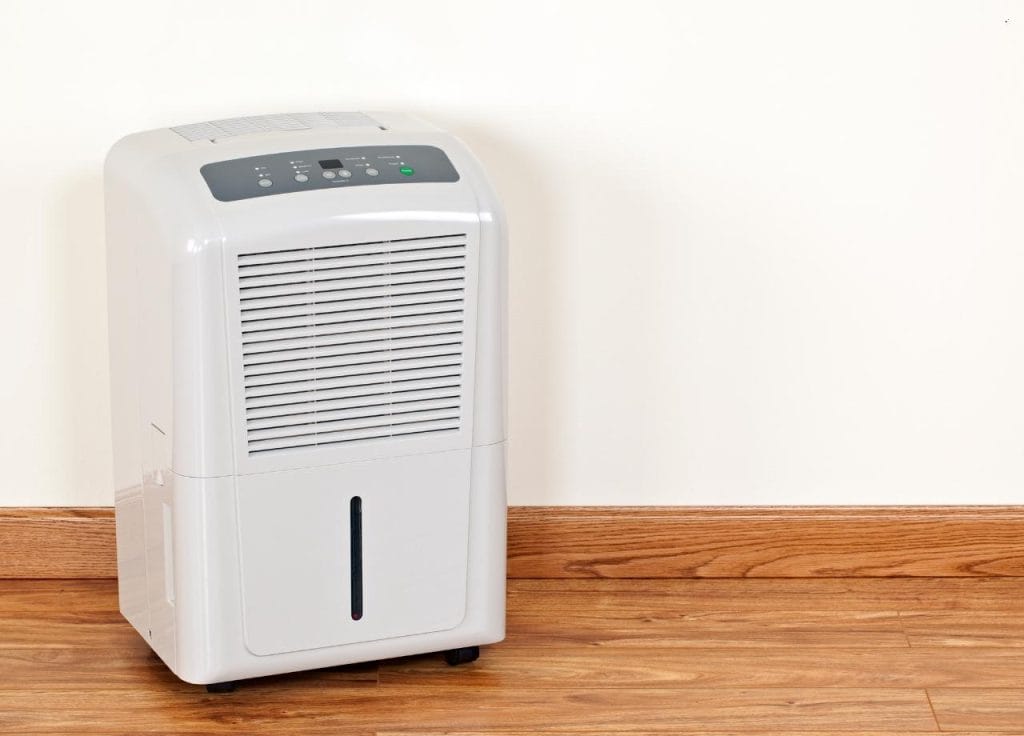
Pros and Cons
They can achieve humidity levels as low as 20–30% relative humidity (RH), creating cleaner, drier environments. Heat from the regeneration process is modest but supports drying. On the downside, they have higher energy use and operating costs, and may emit some warm, dry air that raises ambient temperature.
Ventilation and Air Movers
Moisture-rich indoor air must be replaced or circulated to facilitate rapid drying. Air movers blow continuous airflow over damp surfaces—walls, floors, ceilings—accelerating evaporation into the room’s atmosphere. Once moisture enters the air, dehumidifiers or ventilators remove it.
In some cases, opening windows and using roof-mounted ventilation systems can help, especially when climate and outdoor humidity allow. When conditions are unfavorable, closed-system drying with dehumidifiers and air movers is safer and more predictable.
Heat Drying Systems
Controlled heat sources—including industrial heaters—can improve the air’s capacity to hold moisture. Most effective combined with dehumidification equipment, heat drying allows faster evaporation. It’s particularly useful in colder climates or when materials like concrete, which retain water, are present.
Proper sensors are essential: restoring at optimal temperature and humidity requires monitoring both. Too much heat can damage sensitive materials, while too little keeps drying slow.
Pressure-Differential Drying (Negative & Positive Pressure)
To isolate moisture-laden zones from unaffected areas, professionals use pressure drying techniques. Negative-pressure drying draws air out of impacted zones into dehumidifiers, keeping moisture contained. Positive-pressure drying pushes fresh air into enclosures or cavities, forcing moisture-laden air out.
These methods are valuable when drying behind walls or between floor layers, where moisture can hide. They reduce cross-contamination, help concentrate drying efforts, and protect healthy structures.
Structural Cavity and Injectidry Systems
Injectidry systems deliver warm, dry air directly into cavities to dry framed walls, ceilings, and floors. Tubing is installed into studs or drilled holes, gently forcing moisture out of enclosed areas. Temperature-controlled equipment ensures safety for electrical fixtures and insulation.
Injectidry is useful when removing walls or cutting into structures would be too disruptive or costly. Instead of demolition, targeted drying preserves integrity and helps prevent structural weakening.
Monitoring and Environmental Controls
Drying is a dynamic process—conditions change, and so must equipment settings. Restoration technicians rely on hygrometers, moisture meters, data loggers, and thermal imaging to track progress. Monitoring helps determine when to adjust or remove machinery, preventing over-drying or prolonged exposure.
Setting goals for dryness levels—like reducing drywall to ≤1.5% moisture content or lowering RH to specific ranges—prevents both water-related issues and potential damage from excessive drying.
Phased Drying Approach
A modern structured approach unfolds in stages:
1. Extraction Phase: Removing bulk water with pumps and vacs.
2. Transition Phase: Ambient temperatures rise; airflow and heat are employed.
3. Drying Phase: Dehumidification, heating, and airflow remove remaining moisture.
4. Monitoring & Adjustment: Readings guide repositioning or removal of equipment.
5. Validation and Wrap-Up: Once readings meet targets, systems are shut off and certified dry.
This phased technique (sometimes referred to as the Psychrometric Principle) ensures efficiency, minimizes risk of structural harm, and shortens overall restoration time.
Dehumidification in Various Environments
Cold or Unheated Structures
Refrigerant units lose efficiency in lower temperatures. Desiccant models become essential here. Combined with heaters and proper containment, they deliver consistent drying results.
High-Plaster or Hardwood Components
Dense or porous materials hold moisture deep within. Low humidity, warm air, and extended drying cycles are necessary. Pressure drying and injectidry systems also address moisture in hidden layers.
Containment and Odor Management
Professional projects often create sealed zones to avoid spreading contaminants. Negative pressure helps isolate the drying area. Dehumidifiers inside this zone capture moisture before it affects the rest of the property. Odors from mold or rot are minimized when moisture removal is fast.
Energy Use, Equipment Sizing, and Safety
Professional-grade dehumidifiers draw more power than residential units. Proper assessment of affected area size, moisture amount, and structural materials determines equipment sizing. According to current best practices, dehumidifiers must provide sufficient moisture-removal capacity—measured in pints or liters per day. Improper sizing leads to slower drying or increased operating costs.
Dehumidifier tubes and drainage lines must remain clear. Electrical connections and clearances are crucial to safety. Technicians are trained for setup and are mindful of tripping hazards, drainage leaks, and heat buildup.
Health, Air Quality, and Mold Mitigation
Removing moisture promptly stops mold from forming—typically within 24 to 48 hours of exposure. Dehumidifiers with HEPA filtration reduce airborne spores. Technicians with air scrubbers manage dust and contaminants, ensuring indoor air is safe for returning occupants.
Addressing mold properly prevents allergic reactions and respiratory issues. Continued environmental control until moisture targets are reached is essential for total remediation.
When DIY Isn’t Enough
In small everyday water intrusions—like minor spills—you might use household fans or a portable dehumidifier. Larger-scale incidents demand specialized equipment and technical expertise. Mistakes include:
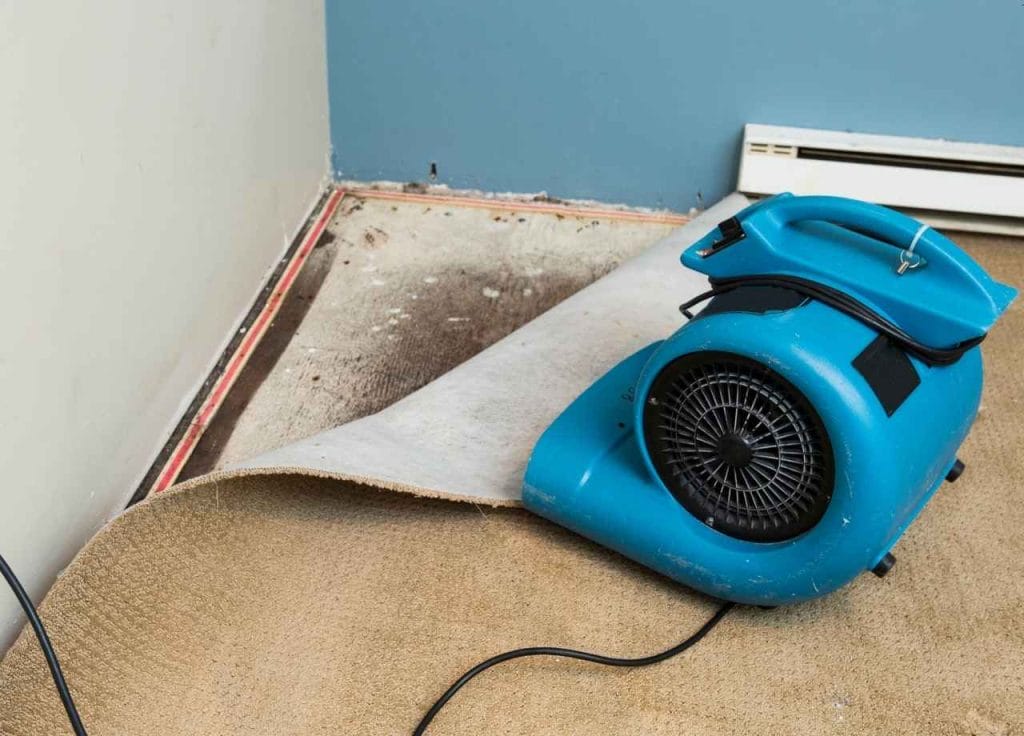
- Using a small home dehumidifier in a basement full of standing water—ineffective.
- Neglecting temperature and humidity oversight—leading to mold.
- Misplacing equipment—parts of a structure may remain wet.
- Operating heaters without dehumidifiers—driving moisture into ceiling cavities.
Professional support ensures thorough drying, documented moisture readings, and reliable results.
Long-Term Prevention
Proper remediation is essential, but long-term measures help prevent repeat incidents:
- Ensure grade and gutters direct water away from foundations.
- Maintain and inspect roofing and flashing for leak vulnerabilities.
- Use moisture-resistant materials like treated plywood in high-risk zones.
- Install humidity sensors or monitors for proactive alerts.
A plan that combines structural remediation with thoughtful design safeguards protects your property with peace of mind.
Final Word
Currently, the field of water damage restoration combines technologies like refrigerant and desiccant dehumidifiers, airflow control, heating systems, cavity drying, and tight environmental monitoring. Techniques evolve with new equipment, sustainability standards, and health-focused workflows. First Coast Contracting deploys these advanced strategies with precision, ensuring thorough, efficient, and safe drying.
When water damage occurs, dehumidification isn’t optional—it’s the backbone of effective restoration. Modern tools and methods deliver results you can trust. In-depth drying, paired with structural stabilization and ongoing prevention, keeps your home safe long after water has receded.